Fluid power systems examples

Control of Fluid Power Systems | SpringerLink
This chapter introduces two system manipulation strategies highly applicable for fluid power systems. Firstly, active damping by pressure feedback, both direct and high pass filtered pressure feedback is shown to significantly increase system damping. Secondly, a...

Fluid Power Systems: A Lecture Note in Modelling, Analysis
Anders Hansen is an associate professor at Department of Energy Technology. He holds a master of science in Electro-Mechanical System Design 2010 (Mechanical Engineering) and a Ph.D. in Energy Engineering 2014 (Investigation and Optimisation of a Discrete Fluid Power PTO-system for Wave Energy Converters) from Aalborg University.

What is Fluid Power?
Fluid power systems generally can transmit equivalent power within a much smaller space than mechanical or electrical drives can, especially when extremely high force or torque is required. For example, a hydraulic cylinder with a 2 in. diameter piston (3.14 sq. in. area) and fluid pressure of 1,000 psi can push with 3140 lbs. of force.

What is Fluid Power | Advantages, Application
Hydraulics uses pressurized liquid, for example, oil or water; pneumatics uses compressed air or other neutral gases. Fluid power can be effectively combined with other technologies through the use of sensors, transducers and microprocessors. A typical fluid power system includes the following components: Hydraulic pump or air compressor

Understanding Fluid Power
A cement mixer, for example, illustrates how different methods of power transmission may be used. Early cement mixers used mechanical drives driven by the truck''s engine or transmission. A system of gears, chain drives and drive shafts provided the speed and torque necessary to rotate the heavy drum of concrete, but speed was difficult to

Basic Diagrams and Systems
This page provides the chapter on basic fluid power diagrams and fluid power systems from the U.S. Navy''s fluid power training course, NAVEDTRA 14105A, "Fluid Power," Naval Education and Training Professional Development and Technology Center, July 2015. Other related chapters from the Navy''s fluid power training course can be seen to the right.

1.1: Introduction to Fluid Power Systems
Describe a basic fluid power system in terms of power conversion. Differentiate between energy and power and give examples of common energy and power units. Determine the energy requirement in ft*lbf to move a 500lbf object 12ft. Determine the power requirement in ft*lbf/s, hp, and W to move a 500lbf object 12ft in 2.3s.

What is Fluid Power
Fluid power systems easily produce linear motion using hydraulic or pneumatic cylinders, whereas electrical and mechanical methods usually must use a mechanical device to convert rotational motion to linear. For example, a hydraulic cylinder with a 2 in. diameter piston (3.14 sq. in. area) and fluid pressure of 1,000 psi can push with 3140

Fluid Power in Robotics: Hydraulic Systems
Here are some examples where fluid power engineering is implemented: Heavy Machinery: Fluid power systems, including hydraulics and pneumatics, offer high power-to-weight ratios and are well-suited for tasks requiring significant force and quick response. They are often more compact than electric systems but can be less precise and more

Fluid Power Systems 15ME72 MODULE 1: INTRODUCTION
Fluid Power Systems 15ME72 Department of Mechanical Engineering, PACE, Mangaluru 3 ADVANTAGES OF FLUID POWER SYSTEM: The advantages of a fluid power system are as follows: 1) Fluid power systems are simple, easy to operate and can be controlled accurately: Fluid power gives flexibility to equipment without requiring a complex mechanism.

Application Of Fluid Power | Application of Hydraulic and Pneumatic
Table summarizes few applications of fluid power. More applications of fluid power. Agriculture – Tractors; farm equipment such as mowers, ploughs, chemical and water sprayers, fertilizer spreaders, harvesters Automation Automated transfer lines, robotics. Automobiles – Power steering, power brakes, suspension systems, hydrostatic transmission

Fluid power
OverviewElementsHydraulic pumpsCharacteristicsApplicationPneumatic and hydraulic systems comparedCommon hydraulic circuit applicationElectrical control
Fluid power is the use of fluids under pressure to generate, control, and transmit power. Fluid power is conventionally subdivided into hydraulics (using a liquid such as mineral oil or water) and pneumatics (using a gas such as compressed air or other gases). Although steam is also a fluid, steam power is usually classified separately from fluid power (implying hydraulics or pneumatics). Compressed

CHAPTER 1: Fundamentals of Fluid Power | Power & Motion
Because fluid power systems have some areas in which fluid is trapped, it is possible that heating this confined fluid could result in part damage or an explosion. If a circuit must operate in a hot atmosphere, provide over pressure protection such as a relief valve or a heat- or pressure-sensitive rupture device.

Fluid Systems: Definition, Types & Examples | Vaia
Fluid Systems Examples. Fluid systems use the force of flowing liquids or gases to transport power. An easy way to understand this is to think about the act of breathing. For a fluid to move, a pressure difference is necessary. We create high-pressure and low-pressure areas every time we breathe that enable air to move in and out of our lungs.

Introduction to Fluid Power | Engineering Library
Fluid power systems can provide widely variable motions in both rotary and straight-line transmission of power. The need for control by hand can be minimized. In addition, fluid power systems are economical to operate. For example, the blade of a bulldozer is normally operated by hydraulic power. Figure 1-1: Force transmitted through fluid.

Modelling Fluid Power Systems | SpringerLink
This chapter introduces modeling of fluid power systems. Two “case” systems, in the form of a motor-valve drive and a cylinder-valve drive, are used to exemplify, firstly, how a lumped parameter time domain model is developed, and secondly, how a linear...

Fluid Power (Part 1) – Hydraulic Principles
working with fluid power systems must know how a fluid power system and its components operate, both in terms of the general principles common to all physical mechanisms and of the peculiarities of the particular arrangement at hand. HYDRAULICS The wordhydraulics is based on the Greek word for water, and originally covered the study

Lecture 1 INTRODUCTION TO HYDRAULICS AND
Examples include pumping stations for pumping water to homes, cross-country gas lines, etc. 2. Fluid power systems: These are designed to perform work. In fluid power systems, work is obtained by pressurized fluid acting directly on a fluid cylinder or a fluid motor. A cylinder produces a force resulting in linear motion, whereas a fluid motor

Hydraulic Systems in the Manufacturing Industry: 8 Equipment Examples
Hydraulic systems are found in equipment at virtually every manufacturing facility, f rom operating robots, forging presses and packaging machinery to powering conveyors.. E nergy is transferred through hydraulic hoses, tubes, and pipes all connected by hydraulic fittings or flanges. T h e power within a hydraulic system is regulated by actuators and valves which
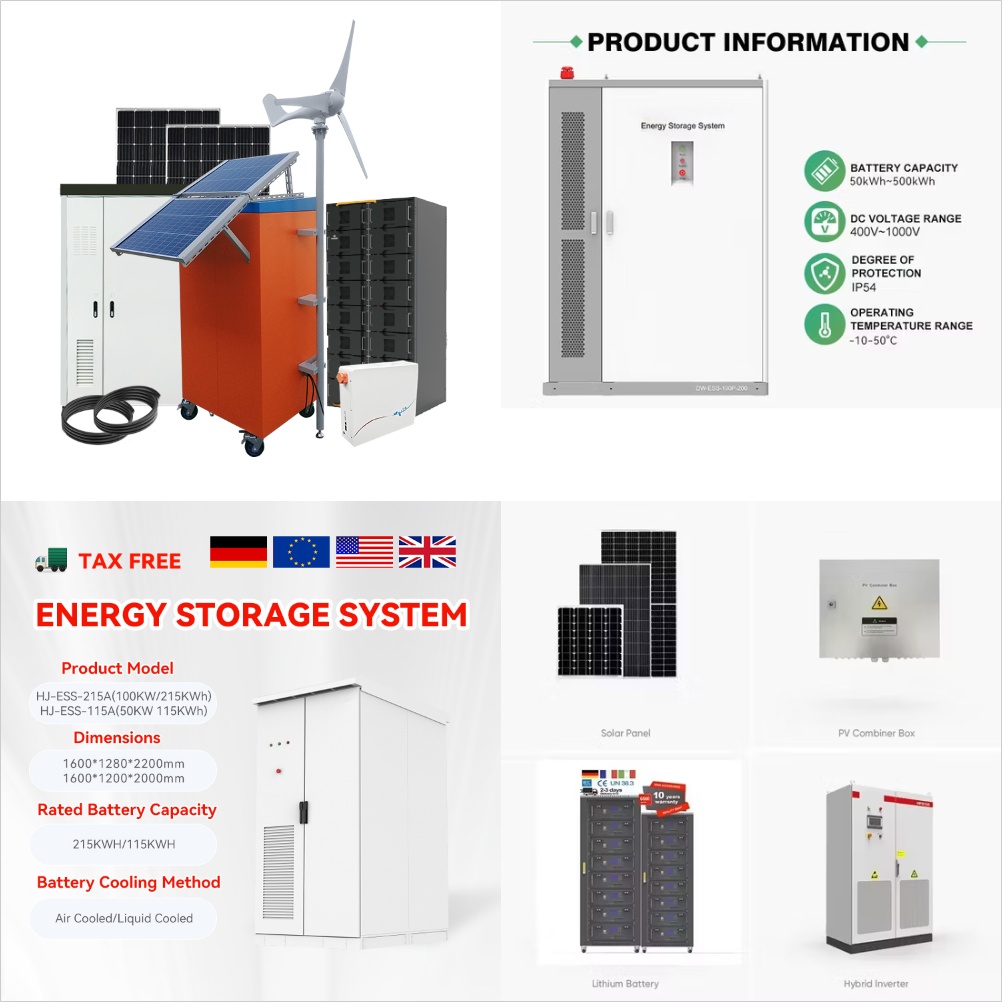
Fundamentals of Fluid Power
Fluid power systems can provide widely variable motions in both rotary and straight-line transmission of power. The need for control by hand can be minimized. In addition, fluid power systems are economical to operate. For example, the blade of a bulldozer is normally operated by hydraulic power.

Fluid power 101 | Essentra Components US
Specifically, fluid power is divided into hydraulics and pneumatics technologies: Hydraulics: the fluid is a liquid, usually oil or water; Pneumatics: the fluid is a gas, typically compressed air. Nitrogen or argon can also be used, but the expense of producing and processing these gasses usually precludes their use; Fluid power systems

What is fluid power?
And fluid power is an important technology. A 2012 study by the Department of Energy discovered that between 2.0% and 2.9% of the United States'' energy is transmitted through fluid power equipment. While that is an impressive statistic, the study also found that the efficiency of fluid power averages 22%.

Fluid Power Pumps & Motors: Hydraulic & Alignment Examples
The Role of Hydraulic Pumps and Motors in Fluid Power Systems In a fluid power system, hydraulic pumps and motors play complementary roles. Acting as the heart of the system, the pump provides the power by transferring fluid under pressure from the reservoir to the system. Using an example of fluid flow:

Fluid power systems : theory, worked examples and problems
Fluid power systems : theory, worked examples and problems Bookreader Item Preview Fluid power technology Publisher London : Macmillan Collection internetarchivebooks; printdisabled Contributor Internet Archive Language English Item Size 464.5M . ix, 212 p. : 24 cm

What is Fluid Power?
Fluid Power is the use of fluids under pressure to generate, control, and transmit power and is subdivided into:. Hydraulics using a liquid such as oil or water, and Pneumatics using a gas such as air or other gases.. Hydraulic principles make up parts of our everyday life, from monitoring the weather to moving heavy objects.

Basic Fluid Power Circuits
Many circuits are used frequently in fluid power systems to perform useful functions. For example, metering circuits offer precise control of actuator speed without a lot of complicated electronics, decompression circuits reduce pressure surges within a hydraulic system by controlling the release of stored fluid energy, and pump-unloading and regenerative circuits

Related Contents
- Fluid power systems pdf
- Two types of fluid power systems
- Simulation of fluid power systems with simcenter amesim
- Hydrocare fluid power systems
- Salami fluid power systems
- Companies using fluid power systems for transportation
- Air power america 5060 topsider multi-purpose fluid removing system
- Can you use power steering fluid in a hydroboost system
- Power steering fluid for toyota solara
- Louisiana power systems
- Big data application in power systems
- Efficient electric power systems